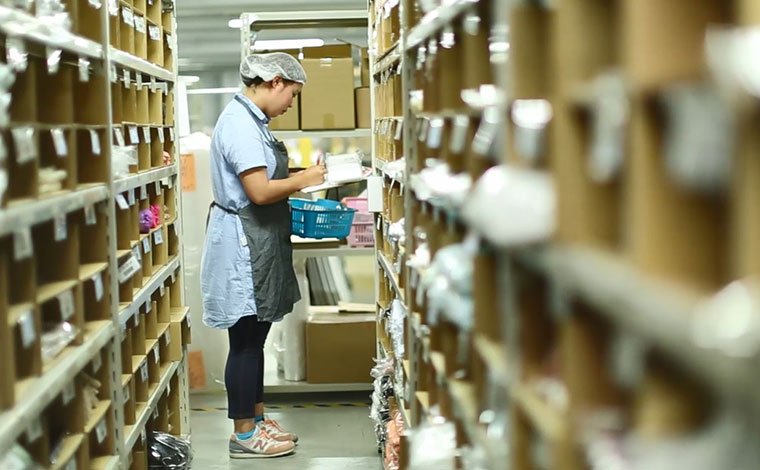
ピッキングとは、伝票や作業指示書に基づいて商品を集める(ピックアップする)ことを指します。正しくピッキングできないと誤出荷につながり、顧客満足度や信頼度の低下を招く恐れがあるため、ミスのないように努めなければなりません。
伝票や作業指示書を目視で確認しながらピッキングを行うとヒューマンエラーが発生しやすくなるため、部分的でも自動化やシステム化をして確実性を高めることも重要です。
本記事では、ピッキングの概要と作業を効率化するコツやシステムについて解説します。
目次
誤出荷と棚卸差異を減らす、
具体的な方法6選!
1物流におけるピッキングとは?
物流におけるピッキングとは、作業指示書(ピッキングリスト)に基づいて保管場所から商品を正しく集める(ピックアップする)業務のことです。ピッキングした商品は、主に以下の手順で出荷準備を進めて発送します。細かい流れはピッキング方法や導入しているシステム、機器によって異なります。
作業指示書(ピッキングリスト)をもとに手作業でピッキングする場合は、正しい商品を選ぶ技量が必要です。ピッキングに時間を消費すると出荷が遅れてしまうため、作業には正確性と俊敏性が求められます。システムや機器の導入で効率化を高めることも検討しましょう。
2物流におけるピッキングの方法
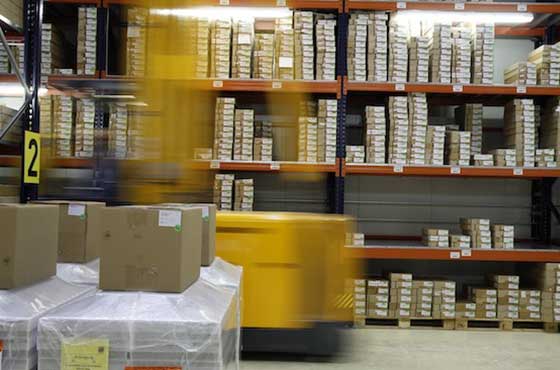
ピッキングは、大きく以下3つの方法に分けられます。それぞれ性質が異なるため、自社に適したものを選ぶことが大切です。
ピッキング方法 | メリット | デメリット |
---|---|---|
シングルピッキング | ・商品の取り間違いが起きにくい | ・移動距離が伸びる ・作業に時間がかかる |
トータルピッキング | ・移動距離を短縮できる | ・仕分けの工程が増える ・作業スペースの確保が必要となる |
マルチピッキング | ・移動距離を短縮できる ・仕分けの工程を削減できる |
・商品の入れ間違いが起こりやすい |
シングルピッキング
シングルピッキングは、注文別にピッキングするシンプルな方法です。商品の取り間違いが発生しにくいメリットがあり、倉庫管理システム(WMS)の活用によって、さらに作業精度を高めることが可能です。
ただし、注文ごとに商品を各保管場所に取りに行く必要があるため、作業時の移動距離が伸びる、時間がかかるというデメリットがあります。
トータルピッキング
トータルピッキングは、複数の注文をまとめてピッキングする方法です。一度にまとめて商品をピッキングできるため、シングルピッキングよりも保管場所への移動回数を減らせるメリットがあり、取り扱うアイテム数が多い倉庫に向いています。
ただし、まとめてピッキングした商品を梱包単位に仕分ける作業工程が増えるため、その仕分け作業を行うスペースを確保しなければなりません。
マルチピッキング
マルチピッキングは、シングルピッキングとトータルピッキングのハイブリッド型で、複数の注文をまとめてピッキングし、同時に仕分ける方法です。1回のピッキングで複数の注文を同時処理できるため、移動距離を短縮し作業効率を高めることができます。
ただし、ピッキングと仕分けを同時に行うため、商品の入れ間違いが発生する場合もあり、徹底した管理が必要です。
3物流におけるピッキングの方法を選ぶポイント
ピッキング方法は、商材、購入点数(シングルオーダーが多いか)などをもとに選定するのが一般的です。その後、以下の後工程も踏まえて最も効率的な方法を検証して決定します。
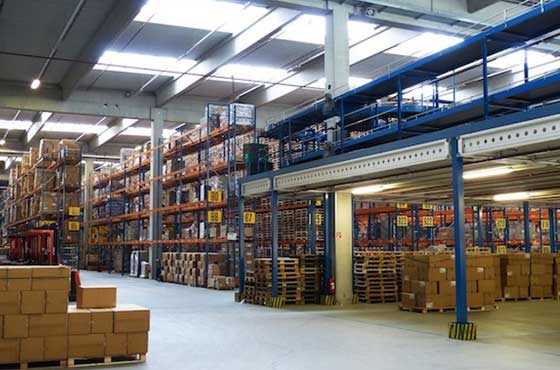
- 単品注文と複数注文の混在比率
- 大型、小型、主力など商品のカテゴリ
- ギフト等の加工有無
自社に適したピッキング方法の選定のために、以下のポイントを明確にすることが大切です。見学した倉庫や他社の方法をそのまま真似をするのではなく、自社にとって効率的な仕組みを考えましょう。
4手作業によるピッキングの課題
手作業でピッキングを行う際の課題は、主に以下の3つです。

- ヒューマンエラーが生じやすい
- 作業時間を浪費しやすい
- 在庫管理が煩雑になりやすい
ヒューマンエラーが生じやすい
作業指示書(ピッキングリスト)を目視で確認しながら手作業でピッキングすると、商品の取り間違いといったヒューマンエラーが生じやすくなります。ピッキングミスは最終的に誤出荷に繋がり、顧客満足度や信頼度の低下を招く恐れがあります。
ヒューマンエラーによるピッキングミスを防ぐためには、システムや専用機器の導入による業務の自動化が効果的です。
作業時間を浪費しやすい
作業指示書(ピッキングリスト)を目視で確認しながら該当する商品を探す、といったアナログ的な方法では、システムや専用機器が導入されている場合と比較すると、作業に時間がかかります。
特に在庫を多く抱える倉庫では商品を探す手間や労力がかかるため、商品の保管場所と出荷作業エリアを往復する工数を含めると、多くの時間を要します。この場合は、シングルピッキングではなくトータルピッキングやマルチピッキングを採用し、時間を短縮できるようにしましょう。
在庫管理が煩雑になりやすい
手作業によるピッキングでは、在庫数の反映がリアルタイムでできないため、在庫管理が煩雑になりやすい特徴があります。そのため、正確な在庫数を把握するための手間や負担も大きくなります。
ピッキングによる在庫管理の煩雑化を防ぐためには、在庫管理システムやバーコードリーダーを導入し、リアルタイムで在庫数の増減を反映する必要があります。
5物流におけるピッキングを効率化するテクニック
手作業によるピッキングを行っている場合は、以下の方法で効率化が可能です。
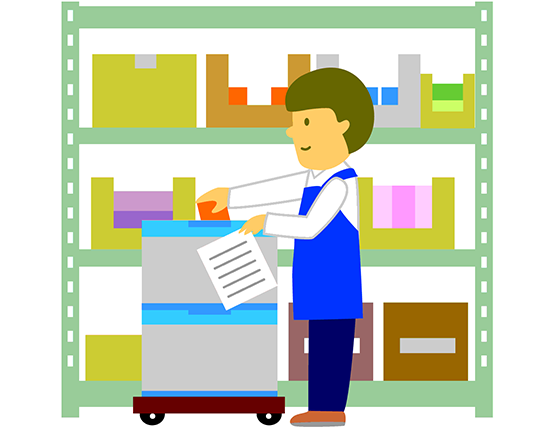
- 作業指示書を最適化する
- 5S (整理, 整頓, 清掃, 清潔, 躾) を重視する
- ロケーション管理を適切に行う
- 物流をアウトソーシングする
- 効率化システムを導入する
作業指示書を最適化する
ピッキングは、作業指示書(ピッキングリスト)をもとに行います。
「最短ルートで商品を集める」「商品が特定しやすい情報を目立たせる」など、作業指示書にさまざまな工夫を施すことでピッキングから梱包までの作業効率が上がります。
作業内容によりますが、倉庫管理システム(WMS)で事前にコントロールすることも可能です。以下は、作業指示書を最適化した2つの事例です。
事例1. オーダーに複数商品がある場合
倉庫へ商品A・B・C・D・Eの出荷指示が来たと仮定します。
このとき保管棚には、A・B・C・D・Eの順番通りに商品が並んでいるとは限りません。そのため、この順番通りにピッキングすると保管棚を行き来しなければならず、作業効率が低下してしまいます。
そこで、事前に倉庫管理システム(WMS)で実際の保管棚の番号順に商品を並び替えて、作業指示書(ピッキングリスト)を出力します。そうすると、最短ルートで商品を集めることが可能になります。
このように「歩かせない・動かさない・考えさせない」は物流設計の基本となります。
事例2. アイテム数・オーダー数が多い場合
アイテム数が多くなると目視確認が難しくなるため、バーコードによる検品が最も効果的です。作業指示書(ピッキングリスト)にバーコードを付与し、ピッキング時に各商品のバーコードを読み込み連動させることで、誤出荷を防止する仕組みが構築できます。
5S (整理, 整頓, 清掃, 清潔, 躾) を重視する
物流現場では、5S(整理・整頓・清掃・清潔・躾)が重要とされています。
5Sは、繁忙期やセール時など注文数の変動によって臨時の作業者が加わった際、いかにミスを少なく抑え、安定したピッキングができるかを左右します。
商品が乱雑に置かれ、どこに何があるのかわからない、備品があちらこちらに散らばっている現場は、ヒューマンエラーが発生しやすい状態です。ピッキング効率も悪くなるため、ロケーションや保管棚に工夫が必要です。
5Sによってピッキングを効率化した事例を2つ紹介します。
事例1. 出庫頻度に合わせた保管でピッキング時間を短縮
定番商品で、日々必ず一定量の出荷がある、キャンペーンやセールにより一時的に大量出荷が見込まれる商品は、ピッキングエリアの中でも出荷作業エリアに近い場所に保管することで、ピッキング時間を短縮できます。
季節によって売れ筋商品が変わる場合は、効率的にピッキングができるように保管場所の配置変更をするなどの工夫をしましょう。
事例2. 商品の置き方でピッキング工程を削減
商品コードは基本的に商品の裏面に印字されます。
そのため、表向きの状態で商品を保管しておくと、ピッキング時に裏返して確認するといった工程が必要になります。そこで、あらかじめ商品コードが見える状態で商品を保管しておくことで、この工程を削減することが可能です。
物流作業をこなしていくのは、最終的に「人」です。全員が5Sを意識して整理・整頓できるようになるためには、普段から重要性を伝え続けていくことが大切です。このように人材教育は物流現場においても重要なテーマといえます。
ロケーション管理を適切に行う
ロケーション管理とは、保管場所に住所(ロケーション)を割り当てることで、どこに商品があるのか把握しやすくなり、探す手間と時間を削減できます。
種類 | 概要 |
---|---|
固定ロケーション | ・商品ごとに保管場所を決め、固定管理する ・保管場所を覚えると作業効率が上がる |
フリーロケーション | ・商品ごとに保管場所を決めず、空き状況に応じて保管場所を変える ・スペースを有効活用できる |
ダブルトランザクション | ・保管場所をピッキングエリアとストックエリアに分ける ・ピッキングを効率化できる |
ピッキング工程の中で商品を探す時間が大きな割合を占めている場合は、ロケーション管理を見直してみましょう。
効率化システムを導入する
ピッキングを効率化するためには、システムやマテハン機器の導入が効果的です。マテハン機器とは、物流全体や工程作業を効率化する作業設備の総称です。ただし、マテハン機器の導入にはコストがかかるため、費用対効果の検証が必須です。
物流をアウトソーシングする
物流の代行業者にアウトソーシングすると、ピッキングを含めた物流業務の委託が可能です。
アウトソーシングすることで、自社物流では導入が難しいシステムや専用機器の環境によって、業務が効率化できるだけでなく、品質も向上するメリットがあります。さらに空いた自社のリソースを商品開発や販促などのコア業務に注力できるようになることで、会社全体の生産性向上にも繋がります。
誤出荷と棚卸差異を減らす、
具体的な方法6選!
6物流におけるピッキングを効率化するシステム
物流では、以下7つのシステムを導入することでピッキングを効率化できます。
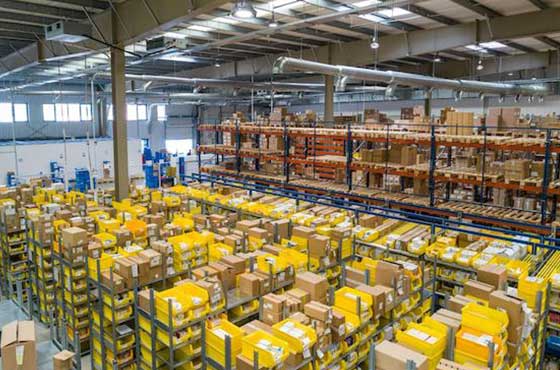
- デジタルピッキングシステム(DPS)
- デジタルアソートシステム(DAS)
- ゲートアソートシステム(GAS)
- ピッキングロボット
- ハンディターミナル
- タブレットピッキング
- RFIDタグ
デジタルピッキングシステム(DPS)
デジタルピッキングシステム(DPS)とは、商品の保管棚に取りつけたデジタル表示器にピッキング対象の商品と数量が表示されるシステムです。作業指示書(ピッキングリスト)を持たなくてよいため、作業効率の向上とヒューマンエラーの抑制を期待できます。
デジタルアソートシステム(DAS)
デジタルアソートシステム(DAS)とは、商品をスキャンすると仕分け先ごとに設置したデジタル表示器に商品の投入数が表示されるシステムです。トータルピッキングを半自動化できるため、ヒューマンエラーの削減を期待できます。
ゲートアソートシステム(GAS)
ゲートアソートシステム(GAS)とは、ピッキングに伴う仕分け作業を補助するマテハン機器です。商品のバーコードをスキャンすると対象のゲートが自動的に開き、デジタル表示された個数分の商品を入れることで仕分け作業を効率化します。
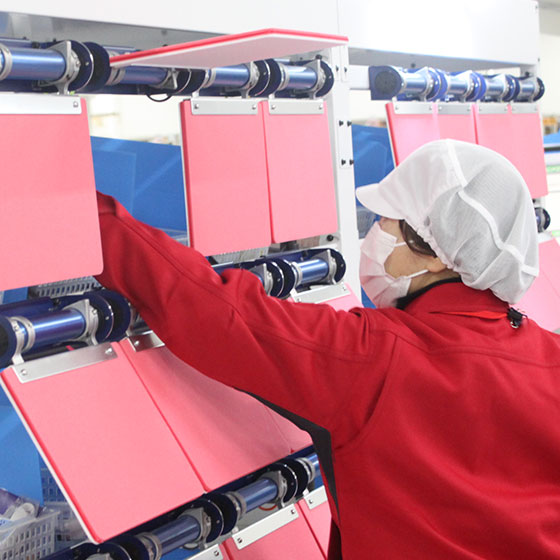
1つのGASに対して複数のゲートを設置することが可能です。
商品を入れ、足元のスイッチでゲートを閉じるまでは次の商品をスキャンできないので、ミスを防ぎながら仕分けることができます。
ピッキングロボット
ピッキングロボットとは、ピッキングを自動化するロボットのことで、以下の種類があります。ピッキングロボットの導入によりピッキングが自動化されると、ヒューマンエラーや工数の削減が可能です。
種類 | 概要 |
---|---|
AGV(無人搬送ロボット) | 床に貼った磁気テープ上を自動で走行し、商品を運搬する |
AMR(自律走行搬送ロボット) | ロボットが自分で走行ルートを決め、自動で商品を運搬する |
GTP(棚搬送型ロボット) | 出荷する商品が保管されている棚を、ピッキング作業員のもとへ運搬する |
ピースピッキングロボット | 指定した商品を自動でピッキングする |
ハンディターミナル
ハンディターミナルとは、バーコードや二次元コードを読み込むことで、商品情報を収集するモバイル端末です。バーコードを読み込むことで在庫の保管場所がわかるため、ピッキングの効率化が可能です。
倉庫管理システム(WMS)と連携することで、ピッキングによる在庫数の変動をリアルタイムに反映することも可能です。
タブレットピッキング
タブレットピッキングとは、タブレット型端末やスマートフォンを活用したピッキングシステムで、ハンディターミナルのようにバーコードの読み込みも可能です。商品画像が表示されるためピッキングミスの削減に効果的です。
こちらも倉庫管理システム(WMS)と連携することで、リアルタイムの在庫情報反映とピッキングの効率化が可能です。
RFIDタグ
RFIDタグとは、電波を通じて非接触でデータを読み込めるタグです。
バーコードや二次元コードとは異なり、RFIDゲートをくぐらせることで一度に複数のタグをスキャンできます。伝票や作業指示書(ピッキングリスト)のバーコードを読み込むことで、保管場所のRFIDタグを点灯させることもでき、商品を探す手間と時間を削減します。
7物流におけるピッキング効率化の事例
物流システムを導入することで、ピッキングを効率化できた事例を2つ紹介します。
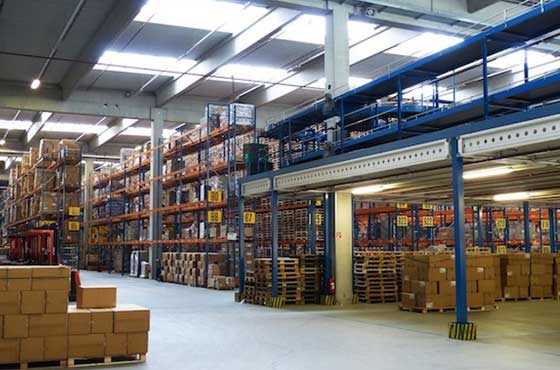
- 自動化システムの導入でピッキングの省力化に成功
- RFIDタグと仕分けロボットの導入で省力化に成功
自動化システムの導入でピッキングの省力化に成功
本事例では、倉庫作業における人手不足やそれに伴う長時間労働、重筋作業が課題となっていました。課題解消のために、RGV(有軌道無人搬送車)を用いた自動倉庫と、AGV(無人搬送ロボット)、ロボットパレタイズ、自動検品を導入。
その結果、自動化システム導入前は計27名で行われていたケースピッキングを、約16名でできるようになりました。導入前の1/3のコストで省力化できたことで、倉庫全体の生産性の向上につながっています。(参考:物流DX導入事例集 P12|国土交通省)
RFIDタグと仕分けロボットの導入で省力化に成功
本事例では、倉庫内作業の生産性向上を目指して、RFIDと仕分けロボットを導入しました。
導入前は、シングルピッキングを採用していたため、作業者が頻繁に保管場所と出荷場所を移動することが課題の1つとなっていました。
これに対し、RFIDと仕分けシステムを組み合わせ、トータルピッキングへ変更。さらに、仕分けロボットを導入することで仕分け作業と運搬工程の省力化を実現しました。
結果、全体の作業品質が向上するとともに、仕分けミスがほぼ見られなくなりました。また自動化に伴う作業の簡略化によって、ピッキングの習得時間が約7割削減できたことも大きな効果といえます。(参考:物流DX導入事例集 P14|国土交通省)
8まとめ:ピッキング業務の効率化により物流品質を高めよう
ピッキングは伝票や作業指示書通りに商品を出荷するために、正確性と俊敏性が求められる重要な工程であることがわかりました。
この工程を疎かにすると、ヒューマンエラーによる商品の取り間違いが発生し、誤出荷や配送遅延の原因となり、最終的には顧客満足度や信頼の低下を招く可能性があることを認識しておきましょう。
当社では、長年の実績から培った知見とノウハウを活かし、業界トップクラスの物流サービスを提供しております。ピッキングに関する課題をお持ちでしたら、お気軽にお問い合わせください。
誤出荷と棚卸差異を減らす、
具体的な方法6選!
サービスはこちら