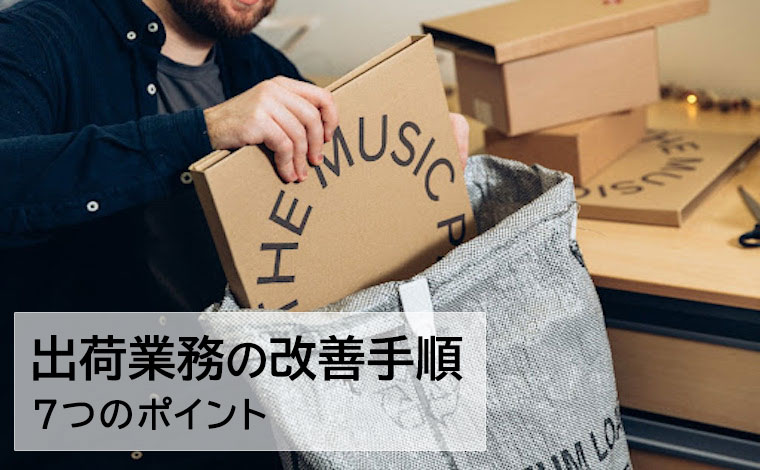
出荷業務は商品を無事に届けるための重要な業務ですが、ミスが発生しやすく、生産性が落ちやすい工程でもあります。
本記事では、出荷業務で起こる問題点や改善のためのポイントを解説します。出荷業務を改善することによる効果や、改善しない場合のリスクなども、是非ご参考ください。
目次
ECショップ運営・ECモール展開に
課題をお持ちの方へ
運営代行サービス資料はこちら
1出荷業務でよく発生する問題例
出荷業務の改善を行う際は、まず自社の出荷工程で発生する問題を洗い出す必要があります。実際の現場で発生しやすい問題は、主に以下の3点が挙げられます。
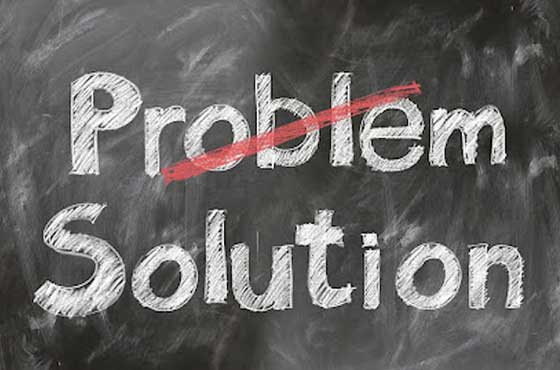
- 注文情報の管理ミス
- ピッキング時のミス
- 発送時のミス
注文情報の管理ミス
注文情報の管理ミスは、システムを使用せず手動で注文情報を管理している場合に起こりやすく、主に以下のようなミスが該当します。
【注文情報の管理ミスの例】
- 数量の確認ミス
- 商品コード・顧客番号の入力ミス
- 備考欄の確認ミス
注文情報の管理ミスは、チェック項目やサービス範囲の見直しをすることで予防できます。
例えば、出荷時における確認項目・手順の整理や、現場の負担を増やさないように、顧客からの要望の対応可能範囲をあらかじめ設定することなどが挙げられます。
ピッキング時のミス
ピッキング時のミスは、倉庫内に保管した多くの商品の中から出荷指示のあったものを集める際に発生します。
【ピッキング時のミスの例】
- カラー・サイズ・商品番号の取り違え
- セット品や景品の封入漏れ
- 数量の取り違え
ピッキングは、受注伝票や出荷伝票の指示に従い商品を探し出す作業ですが、目視で内容を確認していると「出荷伝票の見間違い」や「商品の取り違え」を起こす可能性が高まります。
特に、カラーやサイズのバリエーションが多い商品や、セット品・景品を封入する商品は、ピッキングミスが起こりやすく、ピッキングに慣れたスタッフでもミスを起こす可能性があるので、根本的な対策が必要になります。
発送時のミス
出荷業務ではピッキングを行ったのち、検品・梱包といった段階を踏んでから顧客へ発送します。発送時のミスは、この検品・梱包の際に発生することがほとんどです。
【発送時のミスの例】
- 伝票や納品書の取り違え
- 宛先の取り違え(テレコ)
- 出荷漏れ
検品は発送する商品の品質や、品番・数量を注文情報と照らし合わせるため、多くの手間がかかります。人員が不十分だとミスが発生する可能性も高くなります。梱包は作業フローが煩雑になっていると、宛先の取り違えや、出荷漏れが起こる可能性も否めません。
どのような原因であっても正しく商品が届かなければ、企業の信用やブランドイメージは低下します。小さなミスでも発覚した時点で誤出荷として対処し、対応策を考えましょう。
2出荷業務の改善で得られる効果
出荷業務を改善することで、主に以下3つの効果が期待できます。
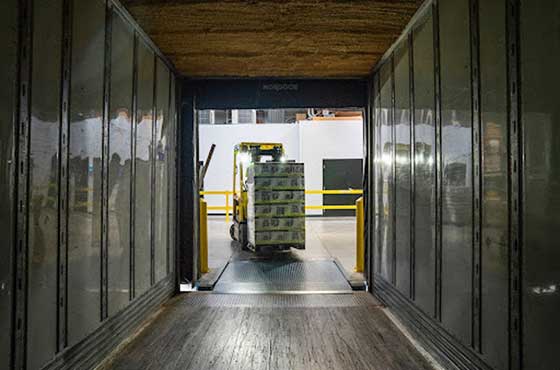
- 業務を効率化できる
- 主要業務に注力できる
- 顧客満足度の向上につながる
業務を効率化できる
出荷業務にミスが多いと、業務プロセスがスムーズに進まないため、業務効率が低下します。業務手順や仕組みを見直すことで作業スピードや正確性が向上し、結果的に業務効率の改善が見込めます。作業工数が少なくなるため人件費の削減にも効果的です。
主要業務に注力できる
規模の小さい企業では出荷業務専門の部署がなく、他の業務と兼務しているケースも少なくありません。出荷業務のミスが続くと、作業時間が余計にかかるだけでなく、クレーム対応も行わなくてはなりません。
出荷業務を改善してミスを減らすことで、ミスの対応にかけていた分のリソースをコア業務に割くことができるようになります。その結果、企業全体の売上向上に繋がるため、利益を出したい企業こそ出荷業務の改善に取り組むべきと言えます。
顧客満足度の向上につながる
誤出荷やテレコ出荷などのトラブルは顧客満足度や信用の低下に直結し、ファンやリピーター離れにもつながります。継続購入を維持するためにも正確で迅速な発送を心がけましょう。
もっとも品質管理を徹底し、正確に商品を届けることは、企業として最低限守るべき事項ともいえます。
ECショップ運営・ECモール展開に
課題をお持ちの方へ
運営代行サービス資料はこちら
3出荷業務を改善しないことで起きるリスク
出荷業務を改善せずに放置していると、現場に時間的・体力的な負担を強いることになります。結果として、以下3つのような問題を誘発する可能性が高くなります。
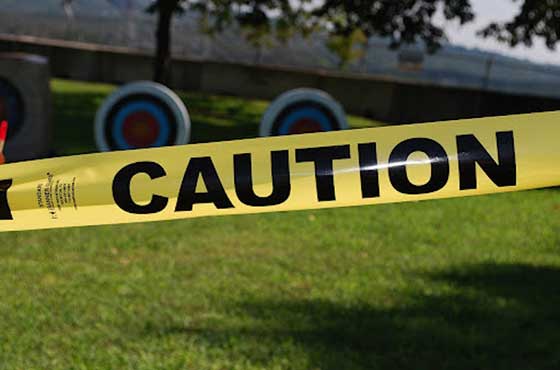
- 個人情報の漏洩
- 在庫過不足による収益の悪化
- 企業の信用低下
個人情報の漏洩
出荷業務で扱う情報には以下のような個人情報が含まれているため、徹底した情報管理を行う必要があります。
【出荷業務で扱う個人情報の例】
- 氏名
- 住所
- 電話番号
- メールアドレス
情報が漏洩し不正に使われてしまった場合、企業としての信頼を失う可能性が高く、最悪の場合は個人情報保護法に抵触する恐れもあります。さらに、クレーム対応やお詫びの連絡などの業務が発生するためリソースを圧迫します。
在庫過不足による収益の悪化
在庫数が多すぎると、在庫管理をする現場スタッフの負担が増えるだけでなく、保管コストの増大やキャッシュフロー悪化などのリスクが生じます。
一方、在庫数が少なすぎると販売や発送ができません。在庫切れで入荷を待っている間に顧客が離れてしまうと販売機会を失います。在庫数が多すぎても少なすぎても収益が悪化するため、適切な在庫管理を徹底しましょう。
企業の信用低下
誤出荷や封入漏れといったミスが多発すると、顧客からの信用は低下します。たとえ商品の評判が高かったとしても、トラブルの多い企業から購入したいと考える顧客は少ないでしょう。
特にECサイトでは「指定日時に到着しない」「不良品が入っていた」などのトラブルがあると、口コミでショップの評価が下がり、売上が低下する可能性があります。
4出荷業務を改善する手順
実際に出荷業務を改善する際は、以下3つの手順を踏むことが効果的です。
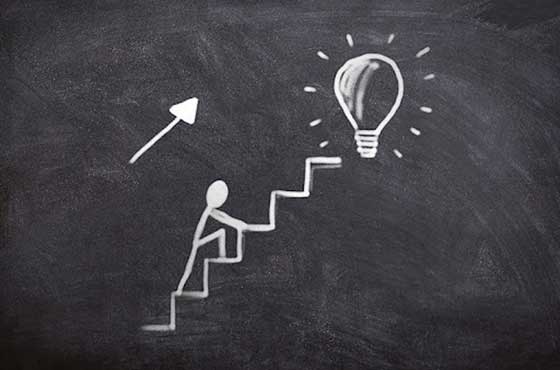
- 現状を把握し問題点を洗い出す
- 改善方法を検討し実行する
- 効果を検証し仕組み化する
現状を把握し問題点を洗い出す
対処すべき問題を明らかにしなければ、施策の効果が出ません。
問題を探す際は、まず出荷業務の作業工程を以下のように分け、工程ごとに作業時間の配分などを確認・検討することで、効率の悪い工程を発見します。
【分類すべき作業工程】
- 注文情報処理
- ピッキング
- 検品
- 梱包
- 積み込み
また、作業にかかわる責任者やスタッフに聴き取り調査を行い、困っていることや不満点を洗い出すことも効果的です。作業手順や時間が把握できたら、集めたデータをまとめて分析しましょう。
分析により、工程ごとの作業時間・作業量・作業人数などの全体像が見えてくるため、作業量を作業時間・作業人数で割った値(作業効率)で比較します。
改善方法を検討し実行する
集めたデータから解決できる施策を検討し、実行します。
問題点 | 解決方法 | 期待される効果 |
---|---|---|
作業手順が明確化されていない | 作業マニュアルの作成と展開 | 業務の標準化 全体の作業効率向上 |
目的の商品を探すのに時間がかかる | 倉庫内レイアウトの見直し | 確認ミスの予防 動線の短縮 |
人手が足りない | システム・マテハンの導入 出荷業務のアウトソーシング |
業務体制の把握 作業工数・時間の短縮 |
1度に複数の問題解決に着手すると効率が悪くなるため、問題が深刻な工程から優先順位をつけて見直していくと、効率良く改善が進みます。
効果を検証し仕組み化する
次に、導入した施策の効果がどの程度出ているか、評価基準(例:出荷数・作業時間・費用対効果)を定めて、効果を検証する必要があります。
一般的に、評価基準には具体的な数値を使いますが、現場担当者の声も重要です。
「負担が軽減した」「残業が減った」などの意見があれば、一定の効果があると評価できます。評価基準を満たし、その施策に効果があると認められた場合は仕組み化して管理します。
ECショップ運営・ECモール展開に
課題をお持ちの方へ
運営代行サービス資料はこちら
5出荷業務を改善する7つのポイント
出荷業務の改善・効率化を行う際は、以下7つのポイントを押さえましょう。
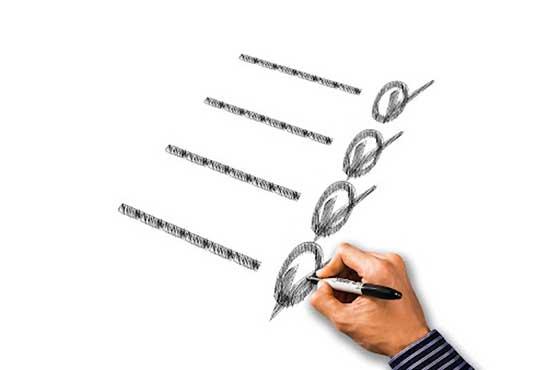
- 最適な人員配置
- 業務の平準化・マニュアル化
- 在庫管理・保管方法の見直し
- 整理整頓・作業スペースの確保
- 作業動線とロケーションの見直し
- 適したピッキング方式の採用
- 在庫管理システムの導入
最適な人員配置
倉庫の管理者がスタッフ一人ひとりの能力や業務量を把握して配置を決めます。業務の負荷を均等に分散させることがポイントです。出荷量に応じた人員配置の調整ノウハウや、スタッフの能力向上を目的としたトレーニング・教育も効果的です。
業務の平準化・マニュアル化
スタッフ個人の作業が属人化すると、進捗管理や問題発見が難しくなります。全体の作業手順を平準化・マニュアル化することで管理がスムーズになり、全体の品質向上も期待できます。
平準化・マニュアル化ができると、教育が必要な新人スタッフでも即戦力として稼動が可能になります。出荷業務をアウトソーシングする際にも、業務手順を伝えやすくなることも1つのメリットです。
在庫管理・保管方法の見直し
在庫の保管スペースが無い、ピッキングに時間がかかる場合は、在庫数と保管方法の見直しも必要です。
倉庫内で縦の空間を活用したり、仕切りや引き出しを利用するなど、無駄のない保管方法で適正在庫を維持できていると、ピッキング作業を効率化できます。
整理整頓・作業スペースの確保
倉庫内の整理整頓ができていないと、誤出荷や取り違えなどのミスが頻発します。普段から商品や資材、備品の保管場所を決め、作業スペースをしっかり確保しておくことがポイントです。
また、検品・梱包時には「作業テーブルには必要なものだけを置く」「作業は1出荷ずつ行う」などのルールが徹底できると、誤出荷や取り違えを未然に防止することができます。
作業動線とロケーションの見直し
広い倉庫で複数の商品のピッキングをする際は、移動距離が長くなり、時間と手間がかかります。この場合、ピッキングを効率化するために、作業動線が短縮できるロケーション配置を意識しましょう。
たとえば、注文頻度の高い商品は取りやすい手前の場所に、セット購入される商品同士を近くに配置すると効果的です。また、色や大きさなどのバリエーションが豊富な商品は取り違えないよう、箱や棚に印をつけることも検討しましょう。
適したピッキング方式の採用
ピッキングには以下2種類の方法があるため、取り扱い商品の種類(SKU)や数量、特性によってピッキング方法を選定し、作業効率を上げるよう意識しましょう。
方式 | 特徴 | メリット | デメリット |
---|---|---|---|
シングルピッキング | 1つの注文ごとに商品をピッキングする | ピッキングした商品をそのまま出荷でき、ミスが少ない | ピッキング時の作業動線が長くなる |
トータルピッキング | 複数の注文の商品をまとめてピッキングする | 作業動線が短く、ピッキング時間を短縮できる | ピッキング後に仕分けするため、ミスが起きやすい |
在庫管理システムの導入
ピッキングや検品などを目視で行う以上、人的な出荷ミスをゼロにはできません。しかし、商品情報や在庫数、伝票の管理をシステム化することで、ミスを最大限に抑えて出荷業務を効率化することができます。
在庫管理システムやバーコード・スキャナーを導入することで、商品情報のデータ管理ができるため、目視確認による人的ミスを削減できます。また、在庫情報をリアルタイムで共有できるため、倉庫拠点が複数ある場合にも効果的です。
6まとめ:出荷業務の改善にはアウトソーシングも手段の1つ
出荷業務の改善は業務の効率化だけでなく、会社や自社ブランドへの信用、顧客満足度の向上にも効果があるため、結果的に売上アップにつながります。
出荷業務の改善を自社で取り組めない場合や、改善に割けるリソースがない場合は、物流業務全体のアウトソーシングを活用することも1つの方法です。
当社では、長年の実績をもとに自社独自のノウハウを活かし、誤出荷率0.0016%以下を誇る物流代行サービスを提供しております。出荷業務の改善に課題をお持ちの際には、お気軽にご相談ください。
ECショップ運営・ECモール展開に
課題をお持ちの方へ
運営代行サービス資料はこちら
サービスはこちら