
倉庫内での出荷作業において「誤出荷が多い」「在庫数が合わない」「倉庫内の保管スペースが足りない」といった問題が頻発している場合、倉庫内の在庫の保管場所が可視化できていないことに原因があるかもしれません。
特に商品の種類が多い倉庫や流動性が高い倉庫では、作業が煩雑でミスにつながりやすくなります。顧客からの信頼を失いかねない出荷ミスを防ぐため、物流倉庫の管理手法を見直しましょう。
本記事では、物流倉庫業務を改善する「ロケーション管理」について、その具体的な方法やメリットを詳しく解説します。
目次
誤出荷と棚卸差異を減らす、
具体的な方法6選!
1ロケーション管理とは
ロケーションとは、位置や場所を示す言葉です。観光施設や飲食店などが建ったとき「立地」の意味で「この場所はロケーションが良い」などと使います。
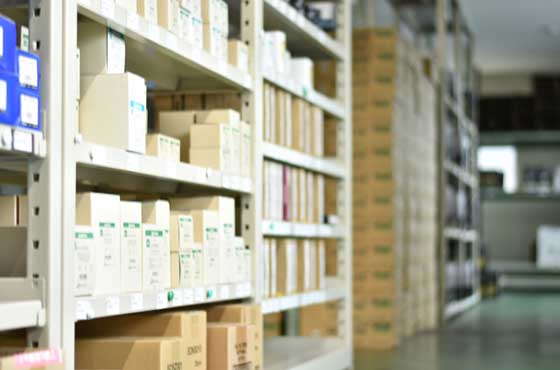
一方、物流倉庫におけるロケーションとは、倉庫内にある商品や商材、原料、資材などが保管されている場所のことです。
ロケーション管理とはそれらの情報をデータとして管理することで、膨大な在庫から1つの商品を見つけ出すのに役立ちます。
ロケーション管理が行われていないと、倉庫内を歩き回って人力で目的の商品を見つけ出さなくてはなりません。ピッキングリストに記された品番を見ながら探し回ることになるので、行ったり来たりする無駄な移動距離が増えて非効率になるだけでなく、誤ってピッキングする可能性も高くなります。
ロケーション管理をすることで、「どこに、何があるか」を瞬時に把握することが可能です。
2適切なロケーション管理を行った場合のメリット
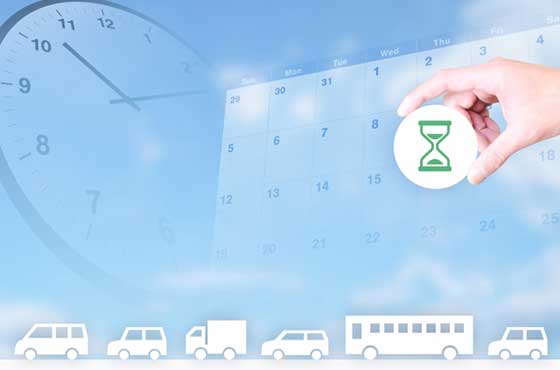
適切なロケーション管理を行うと、商品の保管場所に住所がつくようなイメージで、倉庫内作業の担当者がすぐに商品の所在を把握することができます。
それにより、倉庫内作業の生産性向上につながる下記のようなメリットが生まれます。
作業全体の効率化
ロケーション管理が正しく行われると、ものの住所がはっきりするため、探し回る手間や時間を削減することが可能です。また、経験や勘に頼った属人的な在庫管理から脱却し、誰もが同じレベルで作業できるようになります。
在庫管理や出荷作業の精度向上
商品の保管場所が把握しやすくなることで、各商品の在庫数や状態も把握しやすくなり、在庫管理や出荷作業の精度が向上します。適正在庫を維持し、ピッキングミスも減ることで、販売機会損失の防止や顧客満足度の向上につながります。
誤出荷と棚卸差異を減らす、
具体的な方法6選!
3ロケーション管理の種類
ロケーション管理には、大きく分けて「固定ロケーション管理」と「フリーロケーション管理」と「ダブルトランザクション」の3種類の方法があります。
それぞれ下記のような特徴がありますので、取り扱う商品の種類(SKU)や特性など、自社に合った方法のロケーション管理を採用してください。
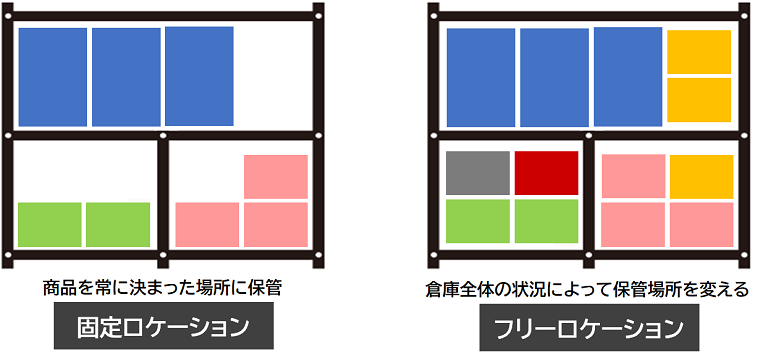
固定ロケーション管理
固定ロケーション管理は、商品ごとの保管場所を決め、常に同じ場所に保管する運用方法です。非常にシンプルな管理方法で、経験が浅くてもすぐに「どこに何の商品があるか」を把握でき、作業効率が上がります。
ただし、スペースが空いていてもほかの商品を保管することができず、デッドスペースが生じやすくなります。季節ごとに商品の入れ替えがある場合などは、定期的なレイアウトの見直しが必要です。
フリーロケーション管理
フリーロケーション管理では、商品の保管場所を固定せず、そのときの倉庫全体の状況に応じて保管場所を決めます。
入出荷の状況によって柔軟に保管場所を拡大・縮小できるので、保管効率のアップが見込め、レイアウトの見直しも不要です。ただし、保管場所が複数に分かれて複雑になりやすいため、システム上で管理する必要があります。
ダブルトランザクション
ダブルトランザクションとは、ストックエリアとピッキングエリアを分け、固定ロケーション管理とフリーロケーション管理を組み合わせる方法です。
例えば、固定ロケーション管理のピッキングエリアと、フリーロケーション管理の保管エリアを作り、ピッキングエリアから商品が出荷されて一定数を下回った段階で保管エリアの商品を移動させます。
保管効率の向上を図りつつ、ピッキング作業の効率化も実現することができます。
4物流の効率化につなげるために
当社ではフリーロケーションを採用しており、主に以下2つに注意して柔軟にロケーション変更しています。
商品の売れ筋状況にあわせて保管
商品の売れ筋状況や、キャンペーン等により特に大量出荷が見込まれる商品を確認した上で、作業者が歩き回らなくて済む近場(保管エリアの手前側)に商品のロケーションを変更します。ほとんど売れない(=出荷が限りなく少ない)商品は保管エリアの中でも「遠い場所」での保管が効率的です。
商品の大きさ種別ごとに保管
「間口・高さ・奥行き」によって商品サイズを大中小の3段階に分け、棚の区分けもそれぞれ3つに分けて準備します。商品の大きさにあわせて棚入れすることで無駄なスペースを削減できます。1SKUごとの在庫数が極めて少ない場合は、ひとつの間口に複数のSKUを保管することもあります。
このように、見た目やサイズなど似通った商品を同じ間口に保管すると、ピッキング時に混同しやすい場合もあるため、商品の特性や荷姿だけで保管場所を決めるのではなく、出荷時のピッキングや仕様を考慮し、最適な保管場所、保管方法を選択することで、物流全体の効率化につなげることができます。
当社の場合は、基本的に1荷主に対して1エリアとなっているため、荷主毎のこだわりを実現するカスタマイズが可能となっています。
5ロケーション管理の基本はロケーション番号
ロケーション管理は基本的にロケーション番号(棚番号)で行いますが、その番号自体にもひと工夫が必要です。
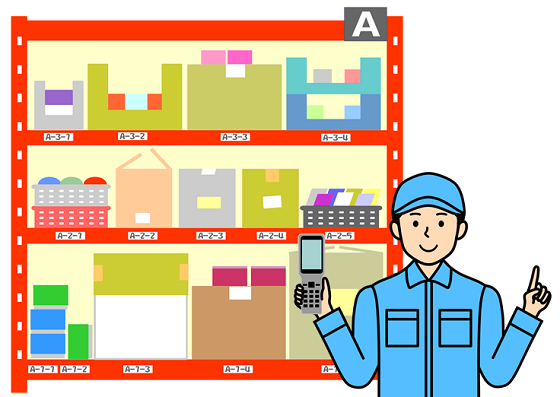
商品名や商品コードをそのままロケーション番号として使うと「経験の浅い作業者がロケーション番号を覚えにくい」「売れ筋商品など、ピッキングしやすい配置に変更できない」といった問題が生じます。
ロケーション番号はシンプルにエリア・通路・列・段などを組み合わせて、そのロケーション番号を聞けばどこに何があるかが瞬時で判断できるように設定しましょう。
そういった工夫によって、下記のようなメリットが生まれます。
<エリア・通路・列・段などの組み合わせでロケーション番号を設定するメリット>
- 商品名や商品コードを知らなくても、誰でも効率的にピッキングできる
- ピッキングの効率化に合わせて柔軟にロケーション設計・変更ができる
誤出荷と棚卸差異を減らす、
具体的な方法6選!
6保管場所・設備の工夫によるロケーション管理の具体策
ロケーション管理を行う際には、下記の6点に注意して保管場所や設備を工夫すると、より生産性の向上が見込めます。自社の倉庫ではどのような改善ができるかをイメージしながら、参考にしてください。
WMSを導入し、バーコード・ハンディターミナルを活用する
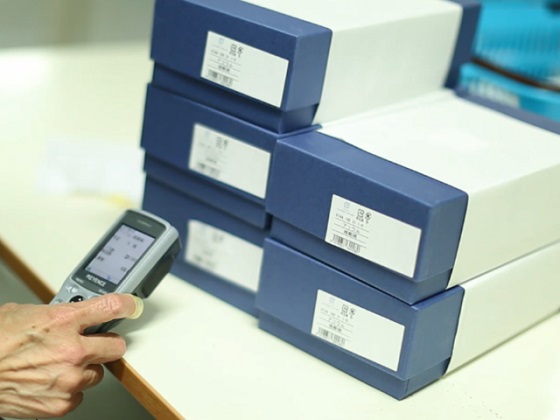
原材料や商品の在庫情報、入出庫情報などを入力して正確な在庫を確認し、過不足のない在庫を維持するためには、WMS(倉庫管理システム)の導入が大きな効果を発揮します。
商品にバーコードを貼付し、ハンディターミナルで読み取るだけで在庫を適切に管理でき、業務が飛躍的に効率化します。
棚の間口の大きさを適切にする
商品を保管する棚の間口は、保管する商品や箱の大きさ、数量などに応じて大きさを決めましょう。搬入・搬出しやすいように間口のサイズを整え、わかりやすいロケ―ション番号を振ることが重要です。
出荷が多い商品は作業場所の近くに配置する
出荷頻度が高い商品は、出荷口や作業場所に近い所に配置するのがポイントです。作業動線を短くすることで業務の効率化が見込めます。
作業効率と保管効率の両立が難しい際はダブルトランザクションを導入する
ピッキングエリアでは固定ロケーション管理を行い、保管エリアではフリーロケーション管理を行うなどのダブルトランザクションを導入すれば、作業効率を高めつつ保管効率の向上を図ることも可能です。
固定ロケーション管理とフリーロケーション管理の両者をうまく組み合わせることで、それぞれのデメリットの軽減が期待できます。
ミス防止のため、似た商品は離れた場所に保管する
見た目やサイズなどが似通った商品を同じ間口に保管すると、ピッキングの際に混同することがあります。商品の特性だけで保管場所を決めるのではなく、出荷時のピッキングや仕様を考慮して最適な保管場所、保管方法を選択すれば、倉庫業務の効率化につなげることが可能です。
不良在庫が多い場合は、フリーロケーションにして1ヵ所にまとめる
売れずに長期間保管されている不良在庫や、商品入れ替えに伴って返品された商品、不良品などが増えると、保管場所が圧迫されます。そのような場合は、フリーロケーション管理ができる場所を確保して、不良在庫の置き場にすると良いでしょう。その際は、必ず内容物を外箱に明記して、ひと目でわかるようにします。
7番号設定の工夫によるロケーション管理の具体策
ロケーション管理を活かせるかどうかは、ロケーション番号の付け方に大きく関わります。次の4点を意識してロケーション番号を設定してください。
歩行する流れに沿って番号をつける
ロケーション番号は動線を考え、作業者が歩行しやすい流れに沿って設定します。これにより、最低限の歩数でピッキングを行うことができ、生産性向上につながります。
棚ごとではなく通路ごとに番号をつける
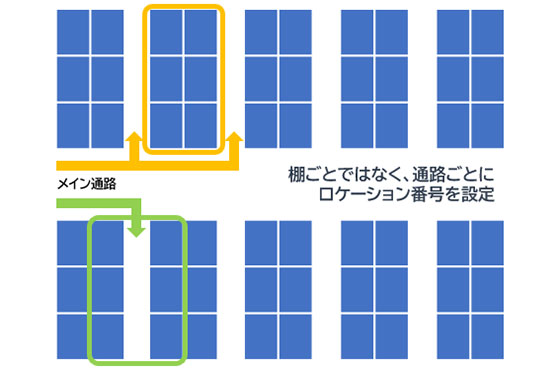
背中合わせに在庫を保管している棚にロケーション番号をつけると、違う通路に同じロケーション番号が存在することになり、作業者が間違った通路に入る可能性があります。
目的の商品に最短距離で達することができるよう、ロケーション番号は通路に設定するのがポイントです。
奇数と偶数でブロックを分ける
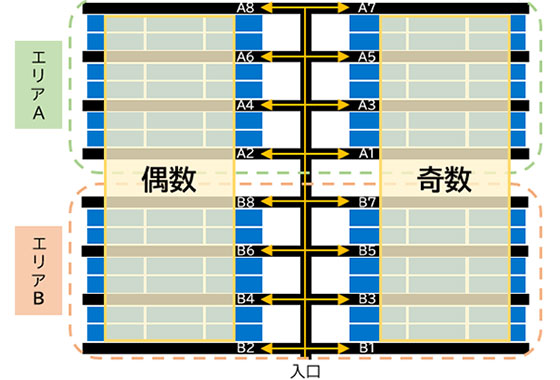
保管場所全体を2つに分け、右側に位置する棚を奇数、左側に位置する棚を偶数などと設定してロケーション番号に紐付けるのも、作業効率化のために有効な方法です。
奇数か偶数かだけでおおまかな位置を把握できるので、担当者が直感的に作業できるようになります。
棚やエリアに色を設定して番号に色の頭文字を入れる
遠くからものの在り処を確認するには、色や絵を活用するのもポイントです。倉庫内をエリア分けして色を振り分け、棚にもそれぞれの場所に対応する色を掲げておき、ロケーション番号の中に色の頭文字を盛り込んでおくと、番号を見ただけで保管場所が探しやすくなります。
8まとめ:ロケーション管理でミスを減らし物流の改善へ
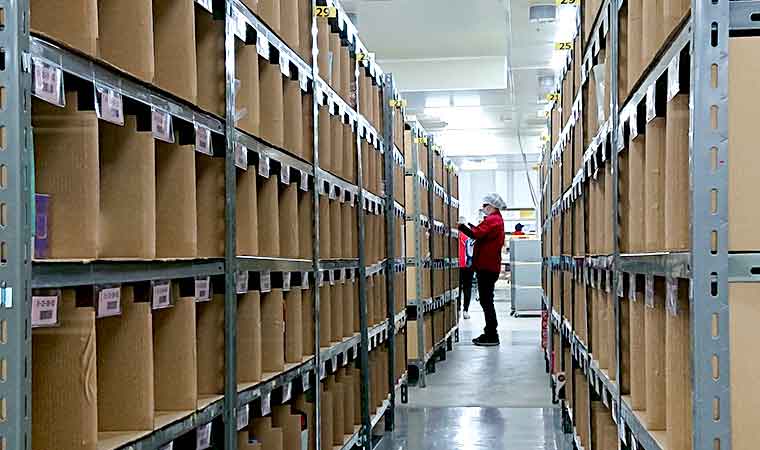
在庫管理やピッキングのミスが積み重なると、顧客からの信頼喪失につながります。
正しいロケーション管理を導入し、保管場所や設備を工夫することで、倉庫内の作業精度を高めましょう。コストパフォーマンスの良い改善策を考えるためには、入荷・検品・棚入れ・ピッキングなどの作業を熟知した物流のプロに倉庫の改革を任せてみてはいかがでしょうか。
当社では、各事業者様の商品の特性や荷姿のほか、出荷時のピッキングや仕様も考慮しながら、最適な在庫管理(ロケーション管理)を実現した物流代行サービスを提供しています。どうぞお気軽にお問い合わせください。
誤出荷と棚卸差異を減らす、
具体的な方法6選!
サービスはこちら